Iscriviti alla nostra newsletter per essere aggiornato/a
sugli ultimi trend e sulle notizie relative a HFLOR/HIMACS.
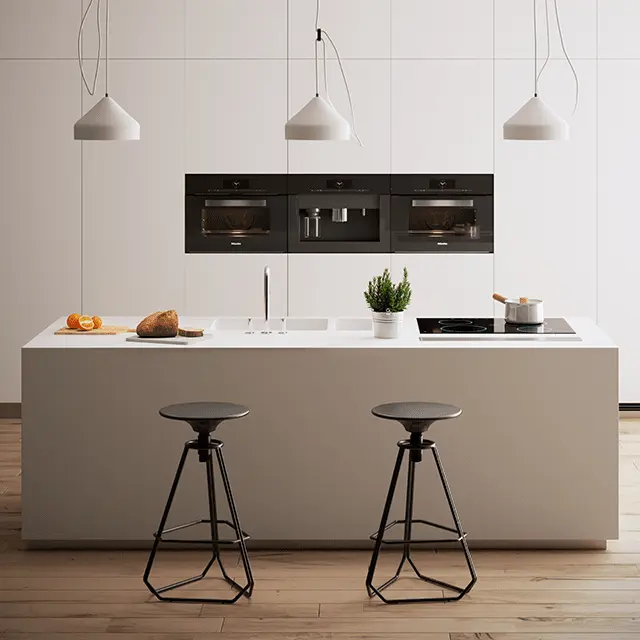
HIMACS: SLO_GEN table
Il tavolo SLO_GEN, realizzato in HIMACS, stupisce i visitatori di Gensler a Los Angeles
Il tavolo SLO_GEN rappresenta il nuovo punto focale della lobby dell'ufficio di Los Angeles di Gensler, ed è il risultato di una partnership innovativa tra Gensler e il Dipartimento di Architettura del College of Architecture and Environmental Design di Cal Poly, a San Luis Obispo (California).
HIMACS è risultato essere il materiale chiave per ottenere queste incredibili e stupefacenti curve, grazie alla sua termoformabilità, resistenza, giunture invisibili e superficie liscia, che hanno convinto sin da subito architetti e ingegneri.
Nel 2011, i professori Jim Doerfler e Mark Cabrinha, co-direttori del Digital Fabrication Lab (“d[Fab]Lab”) di Cal Poly si sono messi in contatto con Shawn Gehle, direttore dell'ufficio progettazione dello studio di architettura Gensler L.A., per creare uno studio totalmente virtuale per la fabbricazione digitale e gli strumenti di collaborazione online.
In risposta, Gehle ha sviluppato un seminario unico nel suo genere, della durata di 10 settimane, per consentire agli studenti di avere accesso ai talenti del design dello studio di architettura e di esplorare le tecniche di ricerca delle forme e fabbricazione digitale attraverso la progettazione di un mobile personalizzato.
La consegna del progetto indicava semplicemente un mobile che potesse adattarsi a un ambiente in cui gli ospiti avessero la possibilità di stare comodamente seduti e in piedi, ma che potesse anche contenere le pubblicazioni di design della società. Il mobile doveva essere concepito espressamente per lo spazio in cui sarebbe stato collocato e distinguersi in modo deciso nel nuovo ufficio Gensler in centro a Los Angeles.
Un prototipo 3D virtuale
Dopo un iniziale incontro, gli studenti di Cal Poly e la facoltà d[Fab]Lab si sono interfacciati con i consulenti Gensler tramite lo strumento di collaborazione online GoToMeeting per condurre le discussioni settimanali previste dal seminario e fare le revisioni del lavoro del team. Oltre a risolvere il problema della distanza di 500 km che separa i designer di Los Angeles e gli studenti della facoltà di San Luis Obispo, questo metodo ha permesso ai professionisti consulenti e agli specialisti dei materiali di partecipare agevolmente alle sessioni e di esporre gli studenti alla collaborazione virtuale che è ormai prevalente nell'attuale pratica professionale. Mantenendo il focus sul flusso di lavoro digitale, anche il processo di progettazione e documentazione del team è stato condotto virtualmente, consegnando un modello 3D per la fabbricazione della tradizionale serie di tavole bidimensionali.
Nel corso del seminario, sono stati sviluppati i progetti originali di tre studenti, per poi ridefinirli utilizzando i software di modellazione 3D Rhino e T-Splines, rivederli virtualmente e ridiscuterli settimanalmente con lo staff della progettazione di Gensler.
Gli ingegneri strutturali dello studio Buro Happold e LX Hausys, il fornitore di HIMACS, hanno affrontato molteplici discussioni per esaminare gli schemi e proporre idee su costruibilità, costi e integrità strutturale. L'incontro finale a Los Angeles si è focalizzato sulla revisione dei prototipi fisici e dei campioni di materiali. Ciò ha consentito al team di affrontare la questione delle sfide poste dalla formatura della vetroresina rispetto alla Pietra Acrilica di Nuova Generazione HIMACS, quale materiale predominante per la superficie del tavolo.
Ispirato dal design e dall'opportunità, LX Hausys è diventato partner del progetto, contribuendo con l'assistenza e le competenze tecniche per il materiale Solid Surface HIMACS, che è risultato essere il materiale ideale per realizzare la superficie avvolgente del tavolo. LX Hausys ha inoltre presentato al team le capacità di R.D. Wing Co. Inc., gli specialisti di Seattle nella fabbricazione, che hanno infine costruito e realizzato concretamente il tavolo.
Il tavolo SLO_Gen è stato recentemente installato all'ingresso principale della sede Gensler di Los Angeles, dove il suo profilo spettacolare continua ad attirare i passanti dalla strada e a suscitare domande sulla sua origine. Grazie alle spettacolari capacità di HIMACS di sposarsi con altri materiali, la combinazione tra il colore bianco del materiale Solid Surface e il legno naturale crea un contrasto delicato ed elegante.
Integrare i pannelli di compensato e il materiale Solid Surface HIMACS
I percorsi di taglio per le nervature in compensato del tavolo sono stati estratti dal modello 3D e tracciati su delle tavole di 1,2 x 2,4 di Europly per la lavorazione con macchine a controllo numerico. Per tagliare le nervature del tavolo sono state necessarie 12 tavole di compensato. Durante il processo di lavorazione, sono state lasciate delle sezioni a incastro lungo i bordi delle nervature per connettere le diverse parti e stabilizzare l'equilibrio.
Queste sezioni sono state infine tagliate, limate e levigate a mano. Con questo processo di fabbricazione si volevano mantenere le forme durante la lavorazione, evitare le vibrazioni e non danneggiare alcuna superficie con nastri o viti. Dopo aver rimosso le sezioni a incastro, le nervature sono state in seguito verniciate e perfezionate con finitura satinata. Una volta che la vernice si è asciugata, il reticolo è stato assemblato a mano, utilizzando un martello di legno e dei dadi.
Termoformatura di HIMACS e integrazione con il legno
Si è iniziato dal piano a forma di S, per cui sono state fresate con una macchina a controllo numerico 4 parti separate. Questo numero era dovuto ai limiti in termini di dimensioni del materiale standard e alle dimensioni complessive dell'involucro del tavolo. I singoli pezzi prodotti sono stati poi incollati e levigati fino all'ottenimento di una superficie perfettamente “piana”, l'unica di tutta la superficie in HIMACS del tavolo.
È stata lavorata una fascia di 1,5 m di larghezza (in pezzi multipli) in modo da seguire la curvatura della superficie del tavolo. Tale fascia è in seguito stata utilizzata come cinghia di sostegno laddove le pareti laterali del tavolo si incontravano con la parte inferiore del piano. Questa fascia è stata incollata nella posizione prevista. Il suo profilo presenta delle ondulazioni lavorate a macchina per agevolare il successivo allineamento delle pareti laterali.
Data la particolarità della curvatura dei pannelli laterali del tavolo in HIMACS, la decisione riguardante le modalità di applicazione dei pannelli e di formatura della superficie si è rivelata di importanza critica. Per questo passaggio è stato necessario determinare quali porzioni di HIMACS potessero essere lavorate a macchina per ottenere la forma senza stampi, per quali invece l'uso di stampi si rendeva necessario e il tipo di stampi richiesti, nonché dove e come applicare i pannelli alla scocca del tavolo per ottimizzare il materiale fornito da LX Hausys.
Per ottimizzare il materiale, aumentare la lavorabilità della Pietra Acrilica di Nuova Generazione e creare i diversi effetti, ogni lato del
tavolo è stato suddiviso in 5 sezioni basate sulla topografia delle singole superfici. R.D. Wing ha creato un mix di stampi, tutti diversi, per fabbricare ogni parete laterale. L'unico modo per ottenere le porzioni più complesse delle pareti laterali con HIMACS consisteva nell'utilizzare uno stampo a valva che consentisse la termoformatura della Pietra Acrilica di Nuova Generazione esercitando contemporaneamente una pressione sulla parte anteriore e posteriore. Per questa tecnica si è reso necessario l'utilizzo di due stampi per ogni sezione da formare, un maschio e una femmina, con una particolare attenzione alla larghezza degli stampi (e quindi a quanto materiale sarebbe stato necessario).
Per creare gli stampi per la termoformatura, R.D. Wing ha impiegato circa 7-9 kg di schiuma di poliuretano avanzata da altri progetti. I lati degli stampi in schiuma sono stati lasciati incompleti, in modo da poter utilizzare lo stampo per ogni sezione fino a 10 volte se necessario. La schiuma è stata montata su una base in MDF e fresata con una macchina a controllo numerico in pile da 1,27 cm. Ogni strato è stato sovrapposto al precedente e lavorato a macchina. Questo processo è stato ripetuto fino alla realizzazione di un intero stampo consentendo di evitare la levigatura. È stata inoltre aggiunta una linea di taglio intorno al perimetro degli stampi per evidenziare come sovrapporre un pannello all'altro. Una volta completata la lavorazione degli stampi e rimossa la schiuma in eccesso, è stato aggiunto uno strato di cotone alla superficie per la dispersione termica.
Per le porzioni più grandi di HIMACS è stato necessario eseguire la termoformatura in due direzioni (curve complesse) e riscaldarle. Una volta riscaldate, sono state inserite nello stampo a valva. Per realizzare tutti i lati sono state utilizzate 12 porzioni singole di HIMACS ottenute con 5 stampi diversi. Il numero di sezioni è stato deciso sulla base dei risultati ottenuti da prove ed errori. Dopo aver dato una forma grezza alle 12 porzioni, sono state reinserite negli stampi per tracciare il profilo per il taglio finale. Ogni sezione è stata tagliata per ottenere il pezzo corrispondente e incollata utilizzando la forma. I pezzi più piccoli sono stati uniti fino a ottenere 5 sezioni principali.
Le parti laterali sono state preincollate fino a ottenere 5 sezioni utilizzabili e poi applicate sui lati della struttura in legno e infine fatte combaciare con la parte inferiore del tavolo lungo la cinghia a fascia della superficie del piano, garantendo una solida aderenza dei lati alla struttura in legno e unendo il tutto per creare le giunture.
Il processo successivo è consistito nel taglio delle parti in eccesso sul fondo e del lato antistante gli scaffali, per poi tagliare dritti i lati con le giunture e creare un bordo piatto da incollare alla parte inferiore del tavolo. Dopo aver incollato la prima sezione alla parte inferiore del tavolo e aver siliconato il retro della prima sezione alla struttura in legno, è stata preposizionata la sezione successiva sulla parte inferiore del tavolo e sulla sezione corrispondente. Con questo approccio è stato necessario tagliare la forma lasciando un minimo spazio vuoto da riempire poi a mano per l'aderenza finale. Una volta fatto aderire saldamente, il processo è stato ripetuto lungo il perimetro.
Dopo aver incollato insieme tutte le sezioni, sono state levigate tutte le superfici esterne. Il passaggio finale è consistito nella levigatura dell'intera superficie e nella correzione di piccolissime imperfezioni.
Una volta fabbricato, l'intero tavolo è stato montato all’interno di una cassa realizzata su misura per il trasporto e la spedizione.
Posizione | Gensler Los Angeles, Los Angeles (California, USA) |
Architecture & Design | Cal Poly, San Luis Obispo, Department of Architecture, College of Architecture and Environmental Design Faculty: Jim Doerfler, Mark Cabrinha Students: Ben Hait-Campbell, Cory Walker, Kegan Charles Flanderka Gensler LA |
Fabbricazione | R.D. Wing Co., Inc. |
Diritti d'autore della foto | ©Gensler Los Angeles |
Comunicato stampa Scarica il comunicato stampa |
Project gallery
-
Scarica immagini
Se siete giornalisti, potete selezionare i media che desiderate e chiederci di fornirveli in HD.
RICHIEDI QUESTA IMMAGINE IN ALTA RISOLUZIONE -
Scarica immagini
Se siete giornalisti, potete selezionare i media che desiderate e chiederci di fornirveli in HD.
RICHIEDI QUESTA IMMAGINE IN ALTA RISOLUZIONE -
Scarica immagini
Se siete giornalisti, potete selezionare i media che desiderate e chiederci di fornirveli in HD.
RICHIEDI QUESTA IMMAGINE IN ALTA RISOLUZIONE -
Scarica immagini
Se siete giornalisti, potete selezionare i media che desiderate e chiederci di fornirveli in HD.
RICHIEDI QUESTA IMMAGINE IN ALTA RISOLUZIONE -
Scarica immagini
Se siete giornalisti, potete selezionare i media che desiderate e chiederci di fornirveli in HD.
RICHIEDI QUESTA IMMAGINE IN ALTA RISOLUZIONE -
Scarica immagini
Se siete giornalisti, potete selezionare i media che desiderate e chiederci di fornirveli in HD.
RICHIEDI QUESTA IMMAGINE IN ALTA RISOLUZIONE -
Scarica immagini
Se siete giornalisti, potete selezionare i media che desiderate e chiederci di fornirveli in HD.
RICHIEDI QUESTA IMMAGINE IN ALTA RISOLUZIONE -
Scarica immagini
Se siete giornalisti, potete selezionare i media che desiderate e chiederci di fornirveli in HD.
RICHIEDI QUESTA IMMAGINE IN ALTA RISOLUZIONE -
Scarica immagini
Se siete giornalisti, potete selezionare i media che desiderate e chiederci di fornirveli in HD.
RICHIEDI QUESTA IMMAGINE IN ALTA RISOLUZIONE -
Scarica immagini
Se siete giornalisti, potete selezionare i media che desiderate e chiederci di fornirveli in HD.
RICHIEDI QUESTA IMMAGINE IN ALTA RISOLUZIONE -
Scarica immagini
Se siete giornalisti, potete selezionare i media che desiderate e chiederci di fornirveli in HD.
RICHIEDI QUESTA IMMAGINE IN ALTA RISOLUZIONE
Image library

Aggiunto alla libreria di immagini
Vai alla pagina Libreria immagini per inviare la tua richiesta, oppure fare clic su OK per continuare la selezione delle immagini.
Contatto stampa
Mariana Fredes +41 (0) 79 693 46 99 mfredes@lxhausys.com
Agnieszka Papież +48 (0) 504 976 688 apapiez@lxhausys.com